ASES – Australia
Unit 8,
5-7 Wiltshire Street,
MINTO, NSW, 2566, Australia
Phone: +61 2 9933 4900
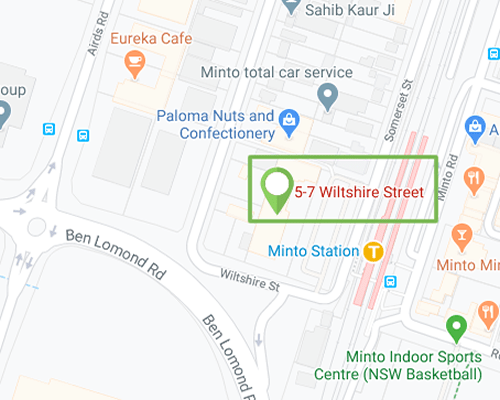
Email Information:
Sales:
info@ases.co
Support:
support@ases.co
Accounts:
accounts@ases.co
General:
info@ases.co
The modular dSPACE SCALEXIO system can be used for hardware-in-the-loop (HIL) and rapid control prototyping (RCP) applications. It is highly scalable, provides high-performance processor technology for demanding real-time requirements as well as comprehensive, precise, and fast I/O capabilities. SCALEXIO systems are configured in dSPACE ConfigurationDesk.
The dSPACE SCALEXIO product line comprises highly flexible and modular systems in various form factors for hardware-in-the-loop (HIL) and rapid control prototyping (RCP) applications for various industries such as automotive, automation, aerospace, medical, transportation, or research. Its powerful real-time technology and comprehensive bus support are ideally suited for the demanding applications of today and tomorrow, which include assisted, highly automated, and autonomous driving, electromobility, and increasing network communication.
SCALEXIO provides two types of real-time processing platforms:
Both real-time platforms provide a high bandwidth Ethernet host interface and IOCNET interfaces for I/O extension or multiprocessor coupling. They also have an angular processing unit (APU) functionality for highly precise angle-based I/O simulation, e.g., injection and ignition signals. With these real-time platforms, up to six independent APUs can be used per SCALEXIO processing hardware.
Depending on the processor, large, complex simulation models can be distributed across several processor cores to ensure that they are computed in real time. A configuration software is used to distribute model parts to the cores and to configure the communication behavior, the simulation hardware, and the model connections.
Multiprocessor support means that several SCALEXIO systems can be interconnected to increase computational power. To provide large bandwidths, SCALEXIO processing hardware can be interconnected via IOCNET. You can use ConfigurationDesk to conveniently model a system.
Communication with the host PC is carried out via Gigabit Ethernet, so the SCALEXIO system can be used in any company network. When more than two processing hardware components are used in combination with a single host PC, they are interconnected via an Ethernet switch to ensure communication. The IP address for the connection can be assigned via a DHCP server or stored on the SCALEXIO system itself.
SCALEXIO offers three types of I/O boards. All the SCALEXIO I/O hardware shares the following characteristics:
Topic | SCALEXIO I/O Boards1) | MultiCompact | HighFlex |
---|---|---|---|
General |
|
|
|
Can be used in | |||
Products |
|
1) No onboard Failure Insertion Unit (FIU), no connection of real or substitute loads.
2) Does not apply to DS633x boards.
The SCALEXIO AutoBox brings the power of SCALEXIO into vehicles such as passenger cars, trucks, trains, and agricultural as well as construction machinery. Optimized for in-vehicle use, it is ideal for test drives when developing components such as electric powertrains and chassis control as well as functions for assisted, highly automated, and autonomous driving.
As a laboratory system, the SCALEXIO LabBox is ideally suited for a wide range of applications, such as RCP, function testing, test bench control, and as a base system for customized HIL setups. The compact chassis fits on an office desk and offers space for up to 18 SCALEXIO I/O boards, which you can easily exchange in order to adapt the real-time system to various applications.