ASES – Australia
Unit 8,
5-7 Wiltshire Street,
MINTO, NSW, 2566, Australia
Phone: +61 2 9933 4900
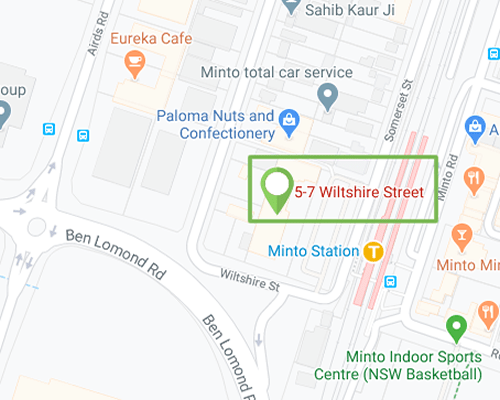
Email Information:
Sales:
info@ases.co
Support:
support@ases.co
Accounts:
accounts@ases.co
General:
info@ases.co
ControlDesk Next Generation is the dSPACE experiment software for seamless ECU development. It performs all the necessary tasks and gives you a single working environment, from the start of experimentation right to the end.
These are some of the tasks ControlDesk can be used for:
ControlDesk unites functionalities that often require several specialized tools. It provides access to simulation platforms as well as to connected bus systems and can perform measurement, calibration and diagnostics on ECUs, e.g., via standardized ASAM interfaces.
Its flexible modular structure provides high scalability to meet the requirements of specific application cases. This gives you clear advantages in terms of handling, the amount of training needed, the required computing power, and costs.
Versions | Description |
ControlDesk | Same tool for rapid control prototyping, HIL simulation, offline simulation, ECU calibration, and diagnostics |
Easy creation of layouts and instruments | |
Synchronous measurement on all data sources | |
Integrated project and experiment management | |
Integrated measurement data management (ASAM MDF 4.1) | |
Compatibility with several ASAM standards (such as ASAM MDF, XCP, CCP, ASAP2, ODX) | |
Powerful tool automation capabilities for user-specific extensions and optimal process integration | |
Access bus network data with instruments (CAN, CAN FD, LIN and Ethernet) | |
Operator mode (protects your projects and experiments against unauthorized changes) | |
Monitoring, logging, and dedicated instruments for CAN and CAN FD | |
Support of virtual validation test scenarios with dSPACE VEOS and SCALEXIO | |
Built-in access to all dSPACE real-time hardware platforms | |
Built-in access to third-party test benches and other hardware by using an ASAM XIL API MAPort server | |
Built-in automation functionality using the ASAM MCD-3 standard | |
ControlDesk – Operator Version1) | For using projects and experiment data that were already created with the standard ControlDesk version |
Protection against altering and creating projects and experiments | |
Built-in access to all dSPACE real-time hardware platforms | |
Built-in access to third-party test benches and other hardware by using an ASAM XIL API MAPort server | |
Additional Modules | Description |
ECU Interface Module | AUD, NBD, JTAG/Nexus, JTAG/OCDS, and JTAG/SDI |
CCP (CAN Calibration Protocol) | |
XCP on CAN, XCP on CAN FD, XCP on Ethernet2) (TCP/IP and UDP/IP) | |
Support of structured data types as specified in ASAM A2L 1.7 | |
ECU Diagnostics Module | Compliance with the ODX database standard (ASAM MCD-2D v2.0.1 and v2.2.0 (ISO 22901-1)) |
Support of ISO protocols for CAN, CAN FD, K-Line, and Ethernet | |
Dedicated instruments for executing diagnostic services and reading or clearing the ECU fault memory | |
ECU flash programming via diagnostic interfaces | |
Support of ASAM MCD-3D v2.0.2 | |
Signal Editor Module3) | For graphical stimulus definition |
Time-synchronous stimulus generation on dSPACE real-time hardware and in Simulink models simulated | |
in dSPACE VEOS | |
Replaying measured data | |
Multiple stimulus patterns can be executed independently | |
Support of the XIL API stimulus format (STZ files, i.e., zipped STI files) | |
Bus Navigator Module4) | Support of CAN, CAN FD, LIN, Flexray and Ethernet buses |
Dedicated instruments for CAN, CAN FD, LIN Flexray and Ethernet bus objects | |
Replaying recorded CAN and CAN FD messages | |
CAN, CAN FD, and LIN monitoring and logging for dSPACE hardware, dSPACE VEOS, and PC bus interfaces | |
Ethernet bus monitoring (dSPACE SCALEXIO, Vector interfaces, Ethernet interfaces of PCs including loopback) | |
CAN bus statistics | |
LIN bus statistics |